What is the best wall system for a home?
We're frequently asked which is the perfect wall system for high-performance LEED, Passive House or Zero Energy Homes, Well, a perfect Answer to that Is, first Ask the Right Questions! - After all, what is the best way to get from one place to another? You have to choose between the quickest way, the safest way, the most scenic way or which route has the most gas stations or least amount of hills. So what is the best wall system? That also depends on what you are looking for.
What is the most durable wall?
What is the most energy efficient wall?
What is the most soundproof wall?
What is the most affordable wall?
That is just a short list of things to consider, and despite many people online saying they have 'the perfect wall' there isn't one right answer, because honestly the perfect wall system for your home is the one that suits the conditions best in the location it's being built and to the budget you have available. Buildings are a complex balance of different elements - of which the walls are only one part.
Also, it's not just about Insulation and efficiency, there are fundamental choices to make depending on where you live in terms of a homes strength. If in an area susceptible to Tornados, Hurricanes or Forest Fires, perhaps it makes more sense to protect your home, family and your biggest investment by opting for something other than timber frame construction like concrete or brick?
So, what is a wall system?
Your wall system is an environmental separator between outside and inside. Its intent is to slow the movement of heat and air between outside and in, and manage moisture infiltration from both sides.
There have been many changes over the previous few decades in building codes, building materials, and how we condition our homes. These changes mean homes are better insulated, more airtight and, most importantly, with better ventilation like HRV's or ERV's or air conditioning. There is also much more understanding of how buildings work and why walls can fail in a home with air conditioning, even when built to code.
For example, if a home is built of timber and will be air conditioned in summer months, it is now agreed on by building scientists that the worst thing you can do is to install an interior polyethylene vapour barrier. Since we build outside with wet materials, buildings start out wet. Over their service life they will continually get wet from the inside and the outside. So forget about trying to 'keep them dry' with a vapor barrier, that's impossible. A wall should be designed so it can dry properly, in both directions.
To build in a cold climate and respect the laws of physics, building scientists agree that a wall needs four major components to be truly successful, and in the following order of importance:
A water control layer of siding, stucco, brick etc - often called the rainscreen:
To protect the exterior surfaces of your home from damage caused by precipitation and groundwater.
An air control layer, or air barrier membrane:
To slow the movement of air through wall assemblies, preventing heat loss and moisture damage caused by condensation in walls.
A thermal control layer, or insulation:
To slow the movement of heat from inside to out in cold months. This is your insulation. It also helps keep heat out of the interior in summer.
A vapor control layer, or vapor barrier:
Although commonly known as a 'vapor barrier' a better term to use would be a vapor retarder. A moisture control barrier should slow diffusion of moisture through walls in either direction without preventing them from properly drying.
Some materials within a wall assembly may serve more than one function, air barriers in particular. Many materials within a wall assembly can slow air flow without trapping vapour.
Option 1) Dense-packed cellulose wall:

This is a wall of offset 2x4s (interior then exterior) with a thick cavity filled with dense packed cellulose insulation. It is recommended to have studs in each wall at 24 inch centers, so when offset you have a stud every 12 inches. The thickness is not fixed, and is completely up to you.
This wall system uses less wood than conventional framing, has low air-infiltration, is resistant to insects and rodents, can be very well-insulated (12 inches or more) with no thermal bridging. To see the choices in lumber for a timber frame building or home, see here.
Keep in mind how important it is that the cellulose be well-packed to avoid settling and leaving you with empty pockets at the top of the walls. For this reason we recommend having it installed by pros, and well-experienced ones.
The addition of a exterior EPS foam sheathing, or alternative choice of rigid insulation panel can reduce any risk of moisture damage, as it brings up the temperature of the exterior condensing surface where the cellulose is. This is an insurance policy that is highly recommended when building like this in the colder more northern regions.
Wood wall framing with 2x4 and 2x6 studs:

This is the most common method of home building, and the one that people in North America & Canada are most used to seeing.
Building codes have greater requirements for thermal performance as of 2012, it is now required in most areas that you break thermal bridges with some form of continuous insulation.
With that, performance has improved, but there is still the matter of an enormous quantity of wood that makes up the frame, so the stated R value of batt insulation does not reflect the performance of a full wall assembly.
Add up all the studs, and without a thermal break you will have a significant portion of your wall that is nothing but solid wood, with an R value of approximately 6 (R1 per inch).
On top of that, unless great care is taken while installing insulation batts, you can easily have small gaps. It takes as little as 1/8th of an inch space between batts and studs to start an air convection and increase the rate of heat loss.
Wood is a renewable resource, so it is very much a 'green' material choice. To improve the performance you can increase the size of studs (going from 2x6 to 2x8) or add several inches of insulation to the exterior.
Mineral wool batts have higher R value than fiberglass, and they are much easier to cut and install properly. To discover the appropriate use of insulation, see our guide to insulation, here.
Prefab homes:

In years past Pre-fab homes were generally just 2x6 framing, and weren't known for high performance, but rather affordability and ease.
In production however they've always had the ability to reduce waste due to the controlled setting of a factory and the abiity to have all cuts are calibrated.
The walls usually come insulated, so they must be kept well protected from rain and snow, or you risk ruining your insulation. The advantages are speed of installation, and a factory precision that is hard to match onsite.
Building codes and a general trend towards smarter building practices has seen some serious leaps forward in the quality offered by pre-fab manufacturers, including high R-value walls and breaking thermal bridging.
There are pre-fab walls that meet LEED standards, and even turn-key prefab homes that have successfully achieved LEED Platinum certification. Pre-fab walls can seriously speed up the building process, and reduce waste as well. Simply find a quality manufacturer, and if you send them your plans, they send you completed wall sections including all your window and door openings.
ICF - Insulated Concrete Forms:
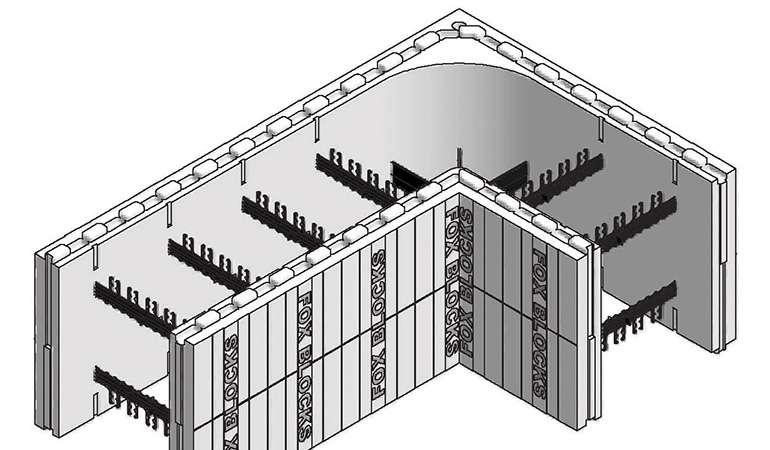
This is a system of polystyrene blocks that are stacked and filled with concrete to form the entire wall system of your home.
Building with ICF blocks is great for reducing sound transmission and stopping the infiltration of air, insects and rodents - as well as being durable for tornados, hurricanes & forest fires.
The thermal performance of ICFs (R Value) is reasonable but not a high end performer unless blocks with thicker foam are used or additional insulation is added to the exterior. The increased performance realized is principally through reduced air leakage, not the R value or thermal mass.
This is a great system that meets the additional challenges of building below grade.
In the interest of saving money and reducing greenhouse gas emissions, we recommend limiting its use above grade, as dollar for dollar you can get much better performance for your money with other wall systems.
That said, an ICF house built on rock could easily be standing for centuries or a millenium, so there is an argument to be made about its full lifecycle, which is great, so long as it is in a desirable location a few generations from now. That can be hard to predict.
Installation requires great care, the biggest risk comes from a ‘blowout’ where a wall section fails. This is not the ideal 'do it yourself' technique, we recommend getting pros.
SIPS- Structural Insulated Panels

Foam SIPS usually consist of a panel made of polystyrene or urethane sandwiched between two sheets of OSB (Oriented Strand Board).
While SIPS with a 5.5 inch foam core were considered a high performer less than a decade ago, increased thermal requirements of building codes and a greater demand for energy efficient homes has brought that wall system back to the category of average.
An excellent long term money saving investment would be to look at thicker SIPS, moving to a 2x8 or 2x10 frame instead of 2x6, offering you a chance at either 2 or 4 additional inches of foam. The relatively small increase in cost will offer a much greater energy performance.
They can be quite airtight if installed correctly; it is important to seal the joints between panels very well and pay careful attention to sealing the joint where the wall meets the roofline. The panel itself is airtight, if the joints are well sealed then the house can be as well.
We would recommend the inclusion of a flexible membrade over the joints to avoid problems with any movement and shifting.
See about getting windows and door openings cut at the factory, otherwise you will likely be using a chain saw on site and will treat your neighbourhood and local environment to a blizzard of little foam balls that you will be finding for years afterwards.
The R.E.M.O.T.E wall
(Residential Exterior Membrane Outside-insulation TEchnique)
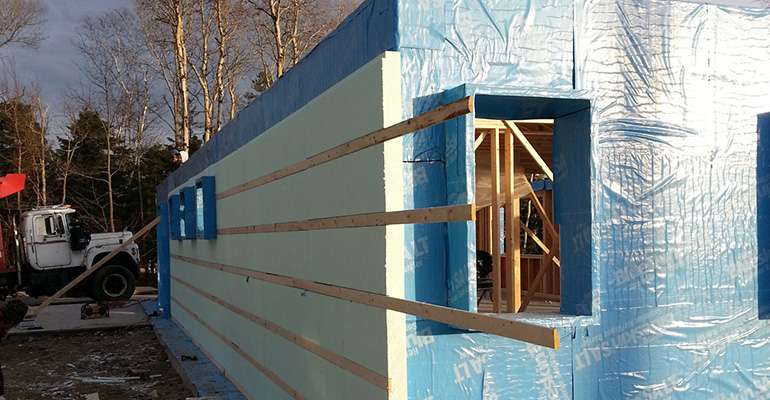
Designed for extreme northern climates, the REMOTE wall was developed by the CCHRC (Cold Climate Housing Research Center) In Fairbanks, Alaska. Walls are framed and sheathed, with the inclusion of a stick-and-peel exterior membrane to control air and moisture movement, and it does so exceptionally well.
With the inclusion of cavity insulation, the vapour barrier in a REMOTE wall is nicely sandwiched about 1/3 of the way through the wall, exactly where it should be. This type of construction is highly praised by building scientists as being among the most durable.
Alternative wall construction methods:
There are many other methods of wall construction, what we have covered here are the more common and cost effective techniques. There are a variety of natural fibres like hemp insulation that are used for home construction and insulation.
-
Larsen trusses in a double-stud wall system: The typical design involves a traditional stick-framed wall with 2x6s and batt insulation in the cavities, covered with sheathing, then I-joists (TGIs) attached to the exterior of the sheathing to allow for seamless insulation with no thermal bridging.
-
Additional material savings can be had when you tape sheathing as the air barrier, by using a high-performance building tape to seal the joints. Taped plywood will not leak air, so you don't need an additional membrane.
-
Larsen Trusses are a cost-effective and lightweight way of creating a double-stud wall assembly without creating problems. As for the sheathing, see here to help decide whether OSB or plywood is the best choice for walls.
-
Hempcrete: a mix of concrete and hemp fibres. It offers great sound proofing, not the greatest R value. It's labour intensive during installation, but an absolutely beautiful textured finish. Hemp wall panels are just finding their way onto the market, and will likely offer significantly reduced labour costs.
-
Log homes: Log home builders speak of the ‘thermal mass’ of wood keeping you warm, but this myth has been dispelled by software energy modelling. They are also highly prone to air-infiltration du to cracks, also known as ‘checking’ and use enormous amounts of wood. Wood has an R-value of somewhere just over 1 per inch, so for an 8 inch wall you are looking at less than R10. So as pretty as they may be, efficient they are not.
Efficient use of constuction materials:
Whatever wall system you choose, when it comes to building floors and walls, the lowest environmental impact in a wood frame construction is with engineered wood (floor trusses, I-beams, jointed wood) . This allows for the use of smaller trees and factory scraps that would often have just been landfill.
Engineered trusses and joists may cost a little more, but they install quickly and accurately with no shimming, compared to solid floor joists which can vary as much as ¼ inch in height. They also facilitate longer spans, allowing for more versatility in floor plan designs.
Like many green building practices, the extra cost upfront for engineered joists will bring you a net savings in the end with time and labour. Engineered floor joists are like roof trusses, a web of 2x4’s. Consequently running plumbing and wiring through those existing openings is a lot quicker than drilling hundreds of holes, so even just financially speaking it makes sense.
Now you know more about building envelopes; to learn more, find all you need in the Ecohome Green Building Guide, or see these pages:
And sign up here for a free Ecohome Network Membership! |
I'm extremely impressed with your writing skills and also with the layout on your weblog. Is this a paid theme or did you modify it yourself? Anyway keep up the nice quality writing, it is rare to see a nice blog like this one these days..
wesdf
Thanks for the feedback, that's nice to hear. The design is ours, but inspired by all the other great sites out there that are easy to navigate.
Regards Mike
Good day. I enjoy your information in helping me make some important decisions about my damn near Passive House.
Yes that's what I call it. Check it out at www.passivehousedesign.ca if you have other insights you can offer.
Cheers
Hi Roy
I had a look over your page, looks great. I'm glad to hear our site helped out, I'm sure we both have insight to offer each other. From where we stand, any and all home construction should begin with planning for solar heat gain in at least some capacity. I hope others check out your site.
Regards,
Mike
Will you elaborate on this paragraph?
"Another material saver would be skipping the sheathing layer all together, using metal cross bracing on the interior (a V shaped metal band that slips nicely into a skill saw cut that you then nail to each stud) and attaching your exterior foam directly to the studs."
I can't visualize this. Can you direct me to a photo or drawing?
Thanks
That can be a bit hard to visualize if you haven't seen it, sorry. I found this image on the web that I think will help that make a bit more sense.
Nice article. What are your thoughts on the wall described below for climate zone 6:
Modified monney wall with 1.5 foil faced polyiso between studs and wood battens. From outside to inside:V inyl siding, WRB, fiberboard sheathing, 2x4 stud bay with r13 insulation, 1.5" foil faced polyiso seams taped and edges sealed with sealant, 2x4 (on side) horizontal battens with r6 rockwool 24"oc , sheetrock.
Interior walls are attached to battens avoiding punturing polyiso which is air barrier and vapor barrier. Electrical and plumbing run between battens to avoid punturing polyiso.
That’s not a ton of insulation, but given that it is 2x4 walls I’m assuming it’s a reno and that’s about all the space you have. The assembly sounds good,especially with the polyiso on the inside since you’ll get more bang for you buck with it when it’s kept warm.
Just a couple of points to maybe think of – When you tape the polyiso try to get a higher quality tape than the cheapest buildings tapes that adorn most homes and building supply store shelves.
Better tapes are less brittle and more flexible, so if there is any movement with the walls (and therefore your polyiso rigid insulation panels) it will help safeguard your air barrier. We’re not huge fans of vinyl siding for ecological reasons, but it does work and it is cheap, there’s no denying that.
There is a product called Steico Universal, a wood fiber board with integrated weather barrier that you may want to check out, it comes out of Montreal,Quebec so depending on where in climate zone 6 you are, it may not be too expensive to ship. We used it recently used it on a demo house and we quite liked it, which is the main photo of this article. it’s a bit more expensive than other brands, but having a 'built-in' weather barrier saves a lot of money in not having to buy and install home wrap.
Thanks for the input! It's actually new construction but I'm not a fan of super thick walls thats why Im looking into 2x4 walls. I feel that proper air sealing and vapor retardance (along with radiant barrier properties of foil) will make up for lack of extra r value. With your experience at what r value does additional thickness become a point of deminishing returns? I know that question could have many answers based on circumstances but do you have a general rule to work with for a very well sealed and thermally broken house in climate zone 6? My best guess without doing the math is total rvalue of walls (minus windows) is around r21 (including radiant barrier factor).
I can see by the comments that there is an interest in a lower cost, super strong, highly insulative assembly that uses a more traditional approach to framing and general building techniques......2x4 construction.....and perfect air barrier characteristics.......has anyone looked at the Shell System assembly?
The photo that you are showing for the SIPS walls actually shows Timber frame and metal insulated panels...
Correct, that's a special case where the load is handled already by the timber frame. Maybe not the best pic to illustrate SiPs then : ) thanks Jeffrey!
light block aloka : What is the best type of building wall?
I have a question. I am trying to build a very energy effiecient home. My retirment home... yeah yeah I know... in this time right now?? i know right.. any ways, loved the info. I had a drawing done by an architect and I wanted to know if you guys could look it over and tell me if I am missing anything or give your input on the wall detail to make it better or last longer with less issues. All the design has been from things I learned on youtube university ( Matt Risinger, and Steve Baczek) or through book I have read. I will try to post picture of wall if I can.
Hi George, if you want to describe your wall assembly on the discussion board page then its open to others to weigh in with thoughts. You could title it "what is the best wall assembly? " and include your location so we know what would work best where you are.
Great article! How does one find an architect and/or GC who is educated in these concepts? I'm in AZ.
Hi Tracy, you could look in the Ecohome green building professionals directory to find quality architects and builders in your region.