Production just started in Quebec of a ground-breaking CMU block that is carbon-negative, thanks to a pioneering Montreal company, Carbicrete, who have developed a new method of producing concrete without cement that effectively makes the product carbon-negative. In partnership with Patio Drummond, a company with over 70 years experience in precast concrete product production, an extraordinary revolution in precast concrete products has commenced in 2021.
What is the problem with cement and concrete?
Portland cement, the most common type of cement used worldwide, is produced by baking a mixture of crushed limestone and other materials to between 1,450 and 1,650 degrees Celsius. These temperatures are most often achieved by burning fossil fuels, and when this limestone is heated, the calcium carbonate inside the rock also releases carbon dioxide.
Cement production is therefore one of the world’s major contributors of carbon dioxide into the atmosphere; according to a 2014 study by the Netherlands Environmental Assessment Agency, this accounts for as much as 10 percent of global emissions.
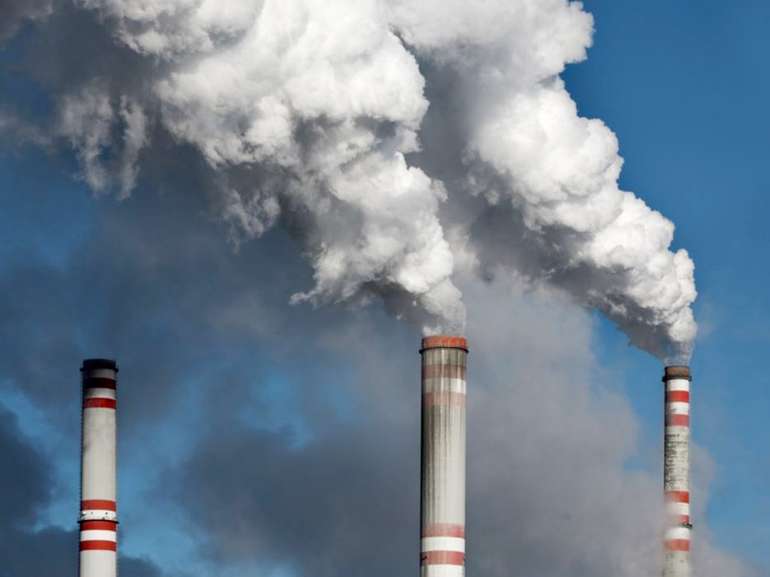
And most of that cement is used to make concrete. Concrete can either be used as ready-mix for onsite pouring and casting purposes, and there are some reduced carbon ready-mix options, like Carboncure Canada.
The other main use of concrete is for precast products – like CMU’s (Concrete Masonry Units, or Cinder Blocks) – and for all manner of construction basics – which we’ve come to depend on for almost every element of our urban landscape. The overall result is that for every ton of concrete produced, approximately one ton of CO2 is released into the atmosphere.
Carbon negative concrete – made in Canada !
In an exciting development, Carbicrete of Montreal, with funding from the Quebec Government, has developed a method of making concrete without cement by replacing it with a by product of steel production, steel slag. Not only does the process avoid the traditional carbon emissions associated with the cement, but the chemical reaction in the production of the new concrete also consumes carbon dioxide, further reducing the net carbon impact of the process.

When carbon dioxide is added to the steel slag and the mixture is put under pressure, it forms calcium carbonate, the ingredient in traditional cement that is currently sourced by baking limestone. The Carbicrete process does not require an external heat source for curing either.
Ideally, carbon dioxide for the production process should be sourced from industrial plants that capture carbon emissions.
The additional bonuses are explained by Chris Stern, Carbicrete’s CEO and co-founder: “The materials (cost) about 20 percent less than traditional concrete, and the concrete is about 30 to 40 per cent better in compressive strength, so it’s actually a better product, it’s the too-good-to-be-true product.”
A new carbon-negative CMU becomes a reality
Theoretical studies in Universities around the world are one thing, and some companies like Watershed Materials' have managed to introduce a market-ready product called the Watershed Block, with up to a 50% reduction in cement and a 65% reduction in embodied energy compared to conventional concrete masonry, which is already a step in the right direction. But it is only when a product like Carbicrete makes it into full commercial production that the benefits start to really add up.

This is where Patio Drummond come into the picture, as the largest manufacturer of poured concrete slabs in North America, and with an annual production of over 1,000,000 CMU blocks – they were the ideal company to ramp up commercialization efforts of this innovative carbon-negative process for manufactured concrete products through an industrial-scale pilot project.
Production has now started for up to 25,000 concrete masonry units (CMUs) daily at their Drummondville, Quebec plant, and Ecohome recently interviewed Chris Stern of Carbicrete and Philippe Girardin, Co-Owner at Patio Drummond.
What will the total impact of this project be? I asked Chris, “A traditional cinder block, known in the construction industry as a concrete masonry unit, or CMU, weights about 18 kilograms, and 2kg of that is cement which equals 2kg of CO2 emitted,” Chris said. “We avoid emitting that CO2, plus the curing process sequesters one kilogram of CO2 per block, so the net result is three kilograms saved per 18-kilogram CMU.”
“As Patio Drummond produce over 1,000,000 CMU per year, if the new Carbicrete CMU blocks were to be produced exclusively in the future, this would result in a minimum 3000 tons per year CO2 reduction” commented Philippe.
To put this into “Press Speak” – this would be equivalent to 6.6 million lbs of CO2 reduction annually – or the equivalent of what 3500 acres of forest can sequester in a year… which we find pretty mind-boggling.
“What we’ve also noticed is that the Carbicrete CMU’s are practically free of efflorescence, because of the updated curing process, which Architects and home-builders really appreciate,” added Philippe.
If you are located in the North East Canada and USA, we suggest checking here for Patio Drummond stockists of the new carbon negative CMU block.
Patio Drummond also intend to investigate expanding the use of Cabicrete for other concrete products, like pavers and slabs, so if you sign up for a free Ecohome membership here, we will make certain to let everyone know when these are available.
Now you know about carbon negative concrete, CMU or Cinder Blocks, read more about how to lower your carbon footprint and build sustainable and energy efficient homes in the Ecohome Green Home Building Guide and in the pages below:
Also, find out about the benefits of a free Ecohome Network Membership here. |
Comments (0)
Sign Up to Comment